- Company announces outcomes of applying “Industry 4.0” technologies such as big data, artificial intelligence and IoT to power plants
- Over 140 experts in power and energy sector including officials from power companies, research institutes and university professors gather to share and exchange the latest technology trends
Doosan Heavy Industries & Construction announced on July 9 that it had held the “Doosan Heavy Industries Energy Technology Forum 2017” at Chung-Ang University in Seoul, bringing together over 140 experts in the power and energy industry, including officials from power companies, research institutes and universities, not to mention Doosan researchers.
This year’s forum, the fifth to date, was held under the theme “Digital Day” with Doosan researchers giving presentations on the achievements made on the three topics that were detailed into 13 sub-topics, including digital solutions and future technology.
Among the various topics, “Solutions for Improvement of Control Functions and Performance Enhancement of Thermal Power Plants” and “System for Real-Time Remote Diagnosis of Turbine/Generator Vibration” drew keen attention from power companies.
Notably, the demonstrations that Doosan researchers gave on advanced digital technologies for power and wind power plants, such as “PreVision,” a system used to predict and diagnose anomalies of plant operation in advance to prevent breakdowns, and “Wind Supervision,” a real-time monitoring & control system for wind turbines, was a particular focus of attention among participants.
Mr. Geewon Park, Chairman & CEO of Doosan Heavy Industries & Construction said, “The forum was held to help secure the much needed market competitiveness, which we hoped to achieve by sharing success stories of applying “Industry 4.0” technology to power plants and by keeping up with the latest technology trends. By converting to digital technology, Doosan plans to incorporate ICT into the entire scope of our business, including design, manufacturing/ construction and services, thereby dramatically improving productivity and quality.”
The forum was attended by officials from Korean power companies, including Korea South-East Power, Korea Midland Power, Korea East-West Power, Korea Southern Power, and Korea Western Power, as well as state-run agencies and state research institutes, including the Korea Institute of Energy Technology Evaluation and Planning, Korea Hydro & Nuclear Power’s Research Center, KEPCO E&C, Korea District Heating Corp., KEPCO Research Institute, and Korea Institute of Machinery and Materials.
Also a number of digital experts in the field shared valuable insights with the attendees: In-jin Choe, a partner at BCG, gave a keynote speech on the power industry’s digital transformation trends; Seo-hoon Jin, Applied Statistics Professor from Korea University, gave a talk on “Case Studies of Digital Data Analysis.”; Byeng-dong Youn, Mechanical and Aerospace Engineering Professor from Seoul National University, gave a presentation on “Diagnosis of Breakdowns”; Sung-bae Cho, Computer Science Professor from Yonsei University, spoke on “Plant Digitalization Through Application of Artificial Intelligence.”
Doosan Heavy Industries & Construction established the “Digital Innovation” unit consisting of the software development team and the data analysis team in 2014, and since then, it has been developing diverse technologies incorporating Industry 4.0.
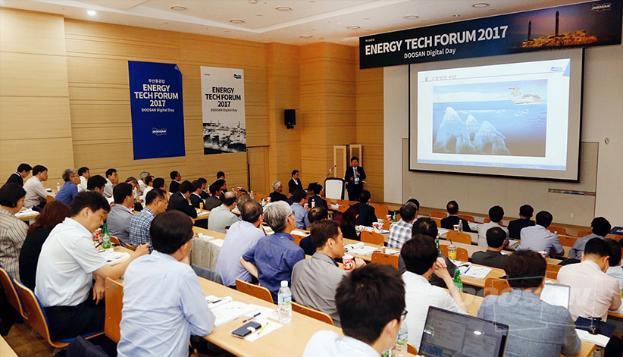
Doosan Heavy Industries & Construction held the “Doosan Heavy Industries Energy Technology Forum 2017,” the fifth to date, bringing together around 140 power & energy experts including officials from power companies, research institutes and universities, as well as Doosan researchers. The company presented research results of applying “Industry 4.0” (e.g., Big Data, artificial intelligence, Internet of Things) to power plants and shared the latest technology trends.
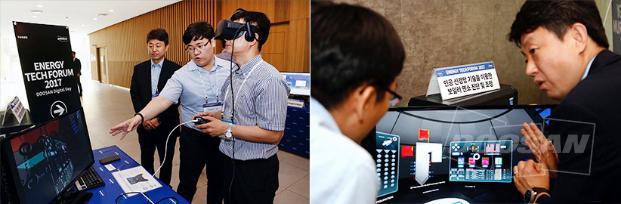
(Left) Participants at the Doosan Energy Tech Forum 2017 demonstrate 3D “virtual reality” technology on “solution for diagnosing and adjusting combustion of a coal-fired boiler.” The equipment allows staff to check combustion situation of boiler and adjust air for combustion supplied to the boiler in a virtual reality environment. The image shown on the monitor is a combustion control.
(Right) Participants at the Doosan Energy Tech Forum 2017 demonstrate a “solution for diagnosing and adjusting the combustion situation of boiler by using artificial neural network technology.”